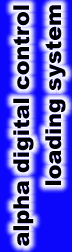
|
Alpha Systems Digital Control Loading System
Our newest control loading system provides absolute realism
Alpha Systems Engineering offers high performance, cost effective control loading systems for use in a wide range of vehicle simulators and training devices. Our control loading systems incorporate state-of-the-art DC servo motor technology to provide absolute realism and the highest degree of reliability at the lowest life cycle cost on the market today. Distinguishing features of the Alpha Control System include tighter integration with the host computer, greater control system modeling flexibility and the use of optical position encoders to provide superior servo control. All control loops are implemented using state-of-the-art digital signal processing and control techniques. This approach supports high fidelity emulation of complex control systems. It eliminates problems associated with analog control electronics, such as parameter drift, which necessitate frequent adjustment and make the application of complex models impractical. The overall design reflects Alpha Systems extensive experience in servo control, flight simulation, dynamic system modeling, software engineering, electro-mechanical design and electronic design.
FIELD PROVEN DESIGN
Predecessors to this system have been installed in F-5E, Hawk MK-53, DC-8-73, B-737-300, PC-9, Beech Baron, C-90, PC-12 and Citation II Flight Simulators.
HARDWARE ARCHITECTURE
A typical control loading system configuration is illustrated in Figure 1. In this case the control loading processor and I/O electronics are integrated directly into the host computer system. This configuration provides outstanding performance and reliability at the lowest cost. The system is also offered in a stand-alone configuration that communicates directly with the host computer over an RS-232 or Ethernet link. The DC servomotors are based on an ironless disk armature. This technology, developed recently for robotics and industrial control applications, yields a number of features that greatly enhance performance in control loading applications. These features include high bandwidth (i.e. fast response to force commands), high torque sensitivity to rotor inertia, very low back EMF and essentially zero torque ripple. These features combine to yield the level of position servo performance required for high fidelity control loading, which previously dictated the use of more expensive (initial cost and maintenance) and less reliable hydraulic actuators. Pulse Width Modulated (PWM) amplifiers provide the servo drive current. These amplifiers provide the most efficient means of AC to DC power conversion and control available. The switching frequency of 25 kHz is well above the audible range and the response of the actuator system. Industry standard mezzanine cards provide all required analog and digital I/O capability. These off-the-shelf modules are attached directly to the control loading processor board to provide high bandwidth access and minimize system complexity.
SYSTEM OPERATION
The basic operation of the system involves measuring the control forces applied by the pilot, simulating the response of the aircraft linkage to the applied force, and using a position servo loop to force the movement of the trainer's control linkage to track the output of the model. This approach, referred to as model following, results in very high fidelity emulation of complex flight control systems. The host computer specifies the control system model, controls the parameters of the model and monitors the status of the system through structured data packets. A set of host interface routines is provided for creating, modifying and interpreting these data packets, and communicating with the control loading system. Execution of the control system model is performed by a Digital Signal Processor (DSP) based single board computer residing on the host computer bus. The high performance floating point DSP runs at a minimum of 40 MHz and is capable of at least 40 MIPS performance. This level of performance provides the capability to simulate complex control systems at high iteration rates. Load cells provide control force feedback. The use of force feedback results in a more realistic compensation of trainer linkage characteristics such as friction and inertia than can be obtained through open loop control of forces. Incremental optical encoders provide precise resolution and low noise position feedback. High reliability and near-zero maintenance are results of our COTS electronics and optical encoder based design.
MODELING APPROACH
Our object-oriented modeling provides the capability of implementing complex control system models including multiple degrees of freedom with minimal development effort. A simplified example of a longitudinal control system model is illustrated in Figure 2.
SAFETY DESIGN FEATURES
- Failsafe system level design.
- Easy on feature prevents violent transients when
amplifiers are first enabled.
- A fault detection routine running on the control loading processor continuously monitors internal state variables
for indications of hardware or software fault conditions
- Redundancy of the encoder and potentiometer position
feedback is exploited to validate position measurements.
- A watchdog timer automatically disables all servo
amplifiers in the event of a hardware or software failure of
the control loading processor.
- Easily accessible kill switches allow the system to be
quickly disabled manually from either the instructor or
trainee stations.
FAA CERTIFICATION
Our control loading systems meet or exceed all requirements of the Federal Aviation Administration's Advisory Circular 120-40B for Phase II. |